Faster, higher, stronger: How the digitalization of industry is redefining value creation
This article titled “Wie die Digitalisierung Wertschöpfung neu definiert” appeared in German last week in the “Größer, höher, weiter (bigger, higher, further)” column of Wirtschaftwoche.
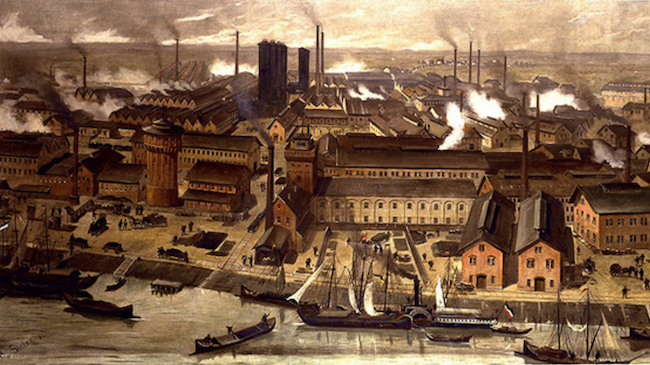
Germany's "hidden champions" – family-owned companies, engineering companies, specialists – are unique in the world. They stand for quality, reliability and a high degree of know-how in manufacturing. Hidden champions play a significant role in the German economy; as a result, Germany has become one of the few countries in Western Europe where manufacturing accounts for more than 20% of GDP. By contrast, neighboring countries have seen a continuous decline in their manufacturing base. What's more, digital technologies and business models that are focused on Industry 4.0 (i.e., the term invented in Germany to refer to the digitalization of production) have the potential to reinforce Germany's lead even more. According to estimates by Bitkom, the German IT industry association, and the Fraunhofer Institute of Industrial Engineering IAO, Germany's hidden champions will contribute a substantial portion to the country's economic growth by 2025 and create new jobs. At the same time, many experts believe the fundamental potential of Industry 4.0 has not even been fully leveraged yet.
The power of persistence versus the speed of adjustment
Most of Germany's hidden champions have earned their reputation through hard work: they have been optimizing their processes over decades. They have invested the time to perfect their processes and develop high-quality products for their customers. This has paid off – and continues to do so.
However, digital technologies are now ushering in a paradigm change in value creation. Manufacturing can be fully digitalized to become part of a connected "Internet of Things" (IoT), controlled via the cloud. And control is not the only change: IoT creates many new data streams that, through cloud analytics, provide companies with much deeper insight into their operations and customer engagement. This is forcing Mittelstand companies to break down silos between departments, think beyond their traditional activities, and develop new business models.
In fact, almost every industrial company in Germany already has a digitalization project in place. Most of these companies are extracting additional efficiency gains in their production by using digital technologies. Other companies have established start-ups for certain activities, or pilot projects aimed at creating showcases. But many of these initiatives never get beyond that point. The core business, which is doing well, remains untouched by all this. And one of the main reasons why is because the people with the necessary IT expertise in Mittelstand companies sometimes are not sitting at the strategy table as often as they should.
Will these initiatives be enough to secure the pole position for Germany's Mittelstand? Probably not. Companies in growth markets are catching up. China's industry, for example, is making huge progress – something that took years to achieve in other places. The role of Chinese manufacturers in the worldwide market is changing: from low-cost workbench to global provider of advanced technology. Market leaders from Germany therefore realize they cannot afford to rest on their laurels.
Competitors from the software side are also reshuffling the balance of power, because their offerings will create a completely new market alongside the traditional business of Mittelstand toolmakers and mechanical and systems engineering companies. If new and innovative companies, such as providers of data analytics, specialized software providers or companies that can bundle complementary offerings, appear on the scene, traditional manufacturing would suddenly become just one module among many – namely manufacturing-as-a-service.
Creating added value in an Industry-4.0 environment often happens when B2B companies integrate B2C approaches, in turn sparking change in their own industry. This requires using agile development processes for continuous improvement and creating a broader portfolio of solutions, for example by increasingly connecting the shop floor with data "from the outside" such as logistics and inventory management. Software that plays an ever-greater role in the "digital factory" of the future will continuously expand its functionalities. Already today, traditional components used in automated industry and made by companies such as Beckhoff, Harting, WAGO, etc. can connect seamlessly to the cloud. Hidden champions from the field of automation technology digitalize their products, enabling their customers to easily join the "smart factory", an environment in which manufacturing facilities and logistics systems are interconnected without the need for a person to operate them. A great example of this kind of digital transformation outside of Germany is General Electric. It is best captured in the words of their CEO Jeffrey Immelt: "If you went to bed last night as an industrial company, you’re going to wake up today as a software and analytics company."
Efficient individualization
The example of Stölzle Oberglas, a leading Austrian glass producer, shows how an industrial company is able to weave the laws of the consumer industry into its own industry. If a customer decides at the last moment (for example due to a large upcoming sports event) to sell a special edition with the name of the winning team on it, Stölzle needs to deliver at short notice. In the past, this would have been cost-prohibitive to do, but in today's digital age, such a highly customized product must not cost more than an off-the-shelf product. Stölzle can afford that because, with the help of software provider Actyx, it has consolidated data from its entire production process, can analyze the data intelligently, and makes it available for the user. In this way, changing specifications can flow into the production process practically in real time using cloud technology. But client-driven innovation in an Industry 4.0 environment doesn't stop here. Actyx uses the insights gained in this project, continues to develop the solution based on those insights, and makes it available to a broader group of users through its solution portfolio. It is similar to what we do at Amazon Web Services too: we develop new features and services based on concrete feedback from customers and then make them available to all our users.
Ecosystem of additional services Knowing how to connect the knowledge of digital native in a meaningful way with engineering knowledge will be critical for hidden champions' future success. Almost daily, new start-ups are formed in Silicon Valley, Tel Aviv, London and Berlin. The business model of many of these new firms is about creating even greater added value for the user of a machine or device: Using sensors that connect machines and products in the "Internet of Things, other services can now also be created that are no longer limited to the assembly line. At the same time, this kind of experimentation poses only a small risk, because in the cloud, services and the exact server capacity can be reserved for each individual application purpose and then paid per use.
These kinds of services are developed by the Berlin-based company WATTx, an independent spin-off from the 100-year-old heating engineer Viessmann. WATTx was created by the company owners to supplement Viessmann's standard products with intelligent digital services, such as an IoT platform for commercial buildings. According to data from sensors inside and outside the building, heater grids, lighting and window shades can be managed remotely. In the meantime, WATTx is doing much more than that. It brings together all of its digital talents in Berlin and gives them unlimited access to new technologies, such as the cloud. On the one hand, this allows ideas to be realized very quickly –or thrown out quickly if they are not achievable. Ideas are also developed and tested here before they hit the market as new companies. In the meantime, Viessmann is developing services on its own that offer added value related to its basic products of heating and thermostats. By working in this way, this traditional German company is able to maintain the contact to end-customers and explore completely new markets.
Keeping an eye on the big changes
Software and services are areas where a producer of a machine or device initially does not feel at home, simply because software and services were never part of its core business. Changing processes that already work seems to be a high risk, at least in the short term. But if the strategic dimension is lacking in Industry 4.0 projects, many companies may not generate any innovative added value at all — neither at the micro- nor macroeconomic level. In the long term, there is a high risk that more agile competitors will take the lead over 'traditional' industrial companies if the latter fail to develop a new path through the global ecosystem of machines, products and (digital) services. But those industrial companies that do take the bold step of implementing new approaches and solutions by embracing cloud technologies will maintain their hard-won status in the German economy. And there's a good chance they will play a more important role in the future.